
Warehouse efficiency is critical for supply chain performance. A well-planned warehouse layout increases throughput, enhances overall capacity, reduces complexity and improves operational efficiency. In this article, we'll explore how an optimized warehouse design—which includes layout, warehouse racking solutions, and technology—can drive substantial improvements across multiple metrics.
Understanding Warehouse Throughput
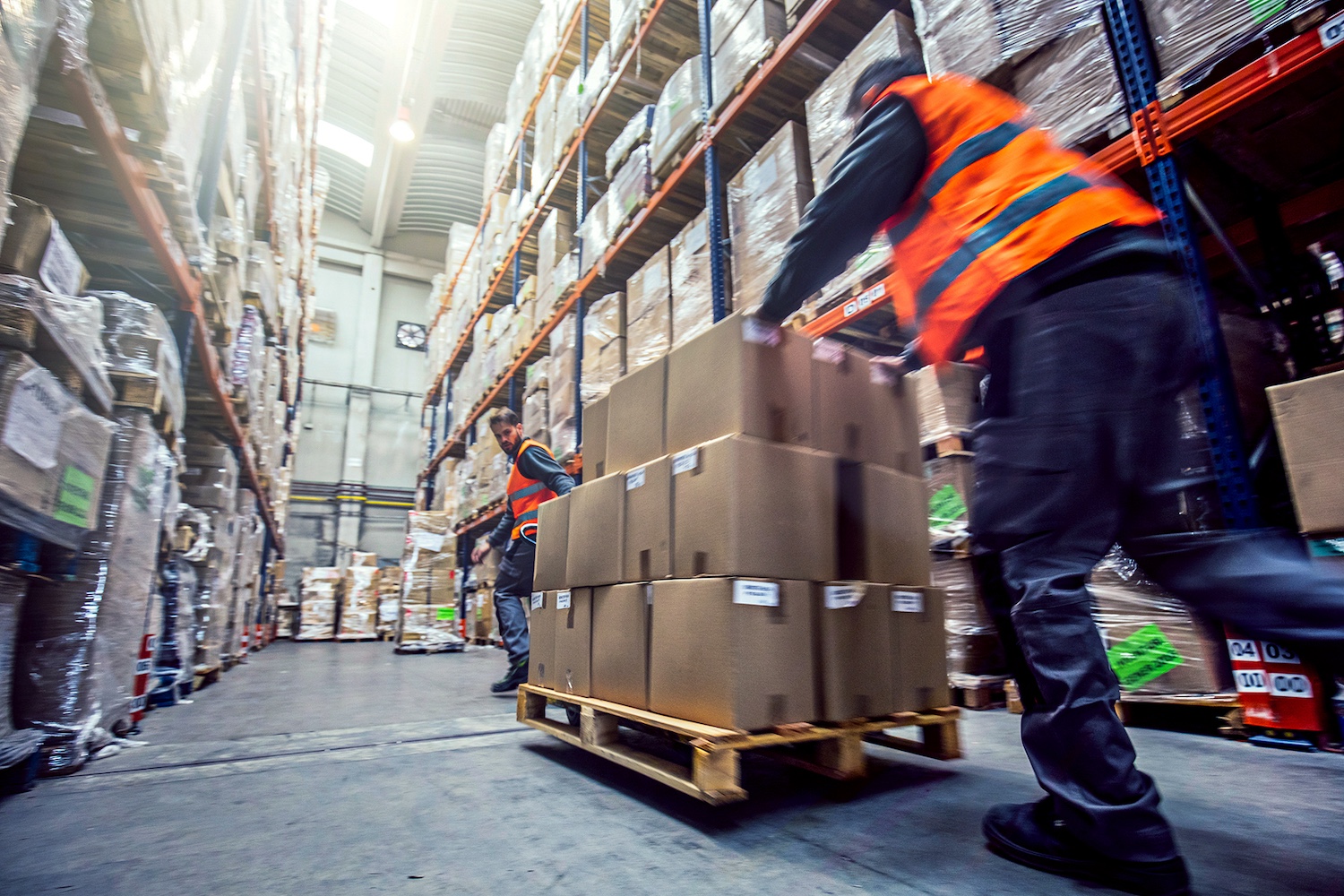
Throughput, a critical measure in warehouse operations, refers to the rate at which products move through a warehouse system. High throughput indicates an efficient system, where goods are received, processed and shipped quickly. Key performance indicators (KPIs) related to throughput include the number of orders processed per hour, order fulfillment speed and inventory turnover rate. Monitoring these KPIs helps identify areas needing improvement and track the effectiveness of any implemented changes to your warehouse racking and layout.
The Principles of Efficient Warehouse Layout
When planning a warehouse’s layout, the goal is to maximize throughput. And layout determines how goods flow through a warehouse, affecting travel time, handling efficiency and storage capacity. Designing for high throughput requires careful planning to minimize delays in workflow and maximize efficiency. Strategies include:
- Workflow optimization: Use warehouse racking solutions to streamline processes, minimize steps and touchpoints. Implementing cross-docking, for example, can eliminate the need for long-term storage by moving products directly from receiving to shipping.
- Minimum travel time: Arrange high-velocity items close to picking and packing areas to reduce travel distance for workers.
- Zone and batch picking: Implement zone picking (grouping similar products together based on demand frequency) and assign employees to specific areas to reduce travel time. Batch picking allows multiple orders to be picked simultaneously, which assures efficiency.
The Importance of Warehouse Racking Solutions
Warehouse racking solutions serves as the backbone of warehouse operations, impacting space utilization, picking and packing times, labor costs and safety. A high-capacity automated warehouse racking system leverages both vertical and horizontal spaces effectively and provides numerous operational benefits:
- Maximum storage capacity: Properly configured racks magnify the use of available space, allowing for as many goods as possible to be stored inside a footprint.
- High operational efficiency: Streamlined access to products reduces picking and packing times, which cuts labor costs and accelerates order fulfillment.
- Safety: Well-designed warehouse racking solutions ensure stability and clears aisles, minimizing the risk of accidents.
- Flexibility and scalability: Modern warehouse racking solutions can be adjusted and expanded to meet changing inventory levels and business growth.
Types of Storage Racks for Warehouses
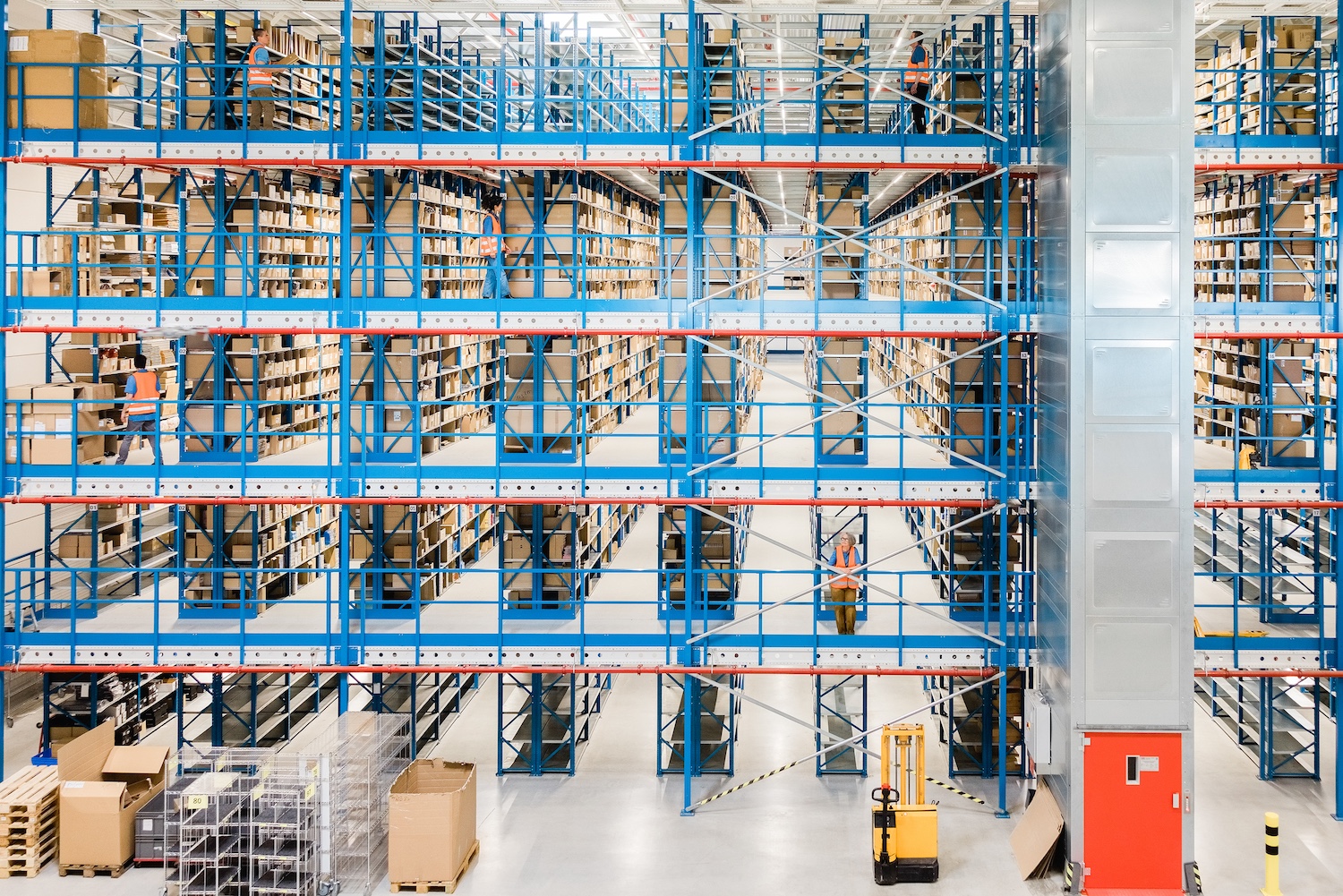
Efficient racking increases space utilization and operational efficiency significantly, so selecting the right system is crucial. Options range from selective racking (which offers easy access to each pallet but lower storage density) to more specialized systems, like drive-in/drive-through racking (designed for similar products in high-density storage), pallet flow racking with gravity rollers (for high-turnover inventory) and pallet shuttle systems (which combine high-density storage with light automation).
Choosing the Right Automated Warehouse Racking System
The selection process begins by assessing a warehouse's specific requirements. Evaluating the specific types of products stored—dimensions, weights, commodity type, turnover rates and picking methods—is the first in choosing the most appropriate racking configuration.
Optimizing space is another critical consideration. Tall racks maximize storage capacity vertically, allowing for ample aisle widths to facilitate forklift maneuverability without compromising storage density.
Technology’s Role in High Throughput
Warehouse racking solutions that include technology can augment efficiency significantly. Robotics, such as automated storage and retrieval systems (AS/RS), manage high-density storage with minimal human intervention, while collaborative robots assist in picking and packing, reducing labor costs and improving accuracy. Conveyance and high-speed sortation can increase throughput and reduce headcount for labor-intensive processes.
In addition to robotics, technology has plenty more to offer:
- Data analytics: Data analytics provide invaluable insights into warehouse operations. Advanced analytics can identify patterns and trends in inventory movement, aiding in the optimization of racking configurations. Predictive analytics can forecast demand and suggest adjustments to accommodate future growth.
- Inventory management systems (IMS): Advanced IMS technology bolsters efficiency further. These systems provide real-time data on inventory levels, locations and turnover rates, enabling continuous optimization of warehouse configurations to align with patterns of changing demand.
- IoT and smart technologies: IoT devices and smart technologies offer real-time monitoring of environmental conditions, inventory levels and equipment status. They enable proactive maintenance, reduce downtime, and ensure continuous and efficient operations.
Warehouse Racking Solutions Capable of Handling Today's Logistics Demands
Similar to the logistics industry as a whole, the dynamic nature of warehouse operations necessitates regular reviews and adjustments to systems. Monitoring KPIs, conducting time studies to identify bottlenecks and soliciting feedback from warehouse staff are essential practices that foster practical insights and enable potential layout enhancements.
Operational efficiency relies on the principles of efficient warehouse layout. Racking configuration and technology are essential to maximize storage capacity and enhance overall productivity. By selecting the right warehouse racking solutions, leveraging technology, and regularly reviewing and adjusting configurations, warehouse operators can create a flexible and scalable environment that meets the demands of modern supply chain operations. Implementing best practices and staying informed about the latest technological advancements will ensure warehouses remain competitive and capable of handling the complexities of today's logistics industry.